Manufacturing - Process
How we make a Jindal TMT 550 Bar - Let's watch this Video
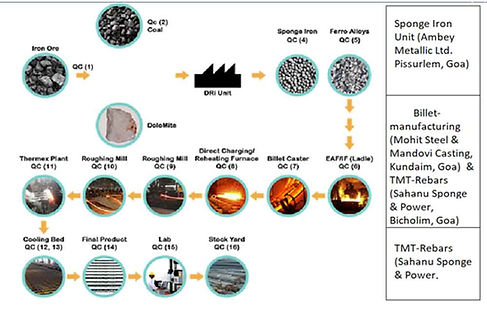
These 3 Factories are within 15-20kms of each other. All controlled & managed by us.
● The first factory imports Iron Ore & Coal from South Africa, to make Sponge Iron.
● The second factory makes Billets as per high chemical standards.
● The third factory makes Steel TMT Bars, branded as ‘Jindal TMT 550’
In our TMT rolling mill plant, the process can be described as:
1. Raw Material – Billets
2. Re-heating in Furnace
3. Roughing or Cogging in Roughing Mill
4. Finishing in Intermediate cum Finishing Mill
5. TMT Cooling Line
6. Cooling on Cooling Bed
7. Inspection, Storage and Dispatch
We manufacture 8 mm to 25 mm TMT Bars as Jindal TMT 550, with strict quality control. (Read More in the 'Quality' section)
The raw material is delivered to our factory every day, for the required daily production. The dispatch of finished TMT product happens every day, as per customer schedule.


Why Jindal TMT 550 over other brands?
1. Guaranteed 500 grade or above, with Test Certificates provided (due to Raw Material from South Africa, as pure Virgin Iron Ore)
2. Highly Cost-effective: 20% more strength, hence quantity of TMT used is lesser
3. Higher Ductility (stability to withstand movements, including higher Elongation)
4. Strict Quality checks & processes to ensure consistency (as per BIS standards) - In Weight per metre, Length & Chemical & Physical properties - such that no cracks are ever observed.
5. Same or next day Delivery
Specific reasons for the Feature Benefits as below:

Higher Strength: Only pure steel billets (using Virgin Iron Ore) are used in Jindal TMT 550. The raw material is from our own group company, chosen specifically for its high Manganese content, as well as lower Sulphur and Phosphorus content. South African Iron Ore we use has Fe content above 65%, which is not possible with Indian-sourced Iron Ore.
Better Elongation & Bending: Superior bendability and easier work-ability are made possible with the unique combination of a tough outer core and softer inner core. Elongation is as high as 20-22%, which is above the ISI standards for Fe550 grade.
Increased Weldability: For Fabrication work on site, Jindal TMT bars are ideal for both lap and butt welding. Their low carbon content ensures optimal strength of the welded joints, without requiring any additional pre- and post-welding treatment.
Corrosion Resistant: Thanks to their Pine and uniform micro structure, Jindal TMT bars do not corrode even when embedded in concrete. This is also because flawless manufacturing ensures that there are no residual torsion stresses in the bars
Fire Resistant: Even at temperatures touching 600 degrees Celsius, Jindal TMT bars display excellent strength and resilience. These qualities act as a safety shield against fire hazards.
Fatigue Resistant: Fatigue in TMT bars begins with accumulation of stress at the root of its ribs, which leads to ‘weakness’. Since Jindal TMT bars are made with accurate uniformed ribs for inherent strength of surface layer that makes Jindal TMT high fatigue resistant bars
PRODUCTION AT A GLANCE
How Jindal TMT 550's Outer & Inner core gets formed

1. Process route of Furnace steel making - Ladle Refining Continuous Casting of Billets ensure the right 7 desired quality with minimal tramp elements & Sulphur & Phosphorus content of 0.090 % Max. Cast Billet are hot rolled in Automatic rolling mill, Which ensure uniform dimensions & properties in each bar.
2. Surface finish of each bar is excellent as the mill employs tungsten carbide rolls against conventional rolls. Each bar is thermo mechanically treated. After leaving the last stand of the rolling mill, the bars are quenched (rapid coiling) in water from final rolling temp of about 1050*c. The Quenching is partial, only until outer surface layer has been transformed from austenite to marten site
3. Because of partial quenching, a part of the original heat remains in the core of the steel and on the coiling bed, this migrate towards the surface and result in an automatic self tempering process where the surface layer of marten site is tempered. The resulting tempered-marten site shows improved deformability compared to as quenched marten site.
4. On atmospheric cooling on cooling bed, Austenitic core is transformed into ductile ferrite - pearlier. The core of the heat treated bars consits of ferrite & pearlier while strong outer layer consits of marten site
